How to Optimize Your Pipeline with Oil Pipeline Sealing Pluggers
Apr 07,2025
How to Optimize Your Pipeline with Oil Pipeline Sealing Pluggers
Table of Contents
1. Introduction to Oil Pipeline Sealing Pluggers
2. Understanding Oil Pipeline Sealing Pluggers
2.1 What are Sealing Pluggers?
2.2 Benefits of Using Sealing Pluggers
3. Optimizing Your Pipeline with Sealing Pluggers
3.1 Installation Techniques for Sealing Pluggers
3.2 Ma
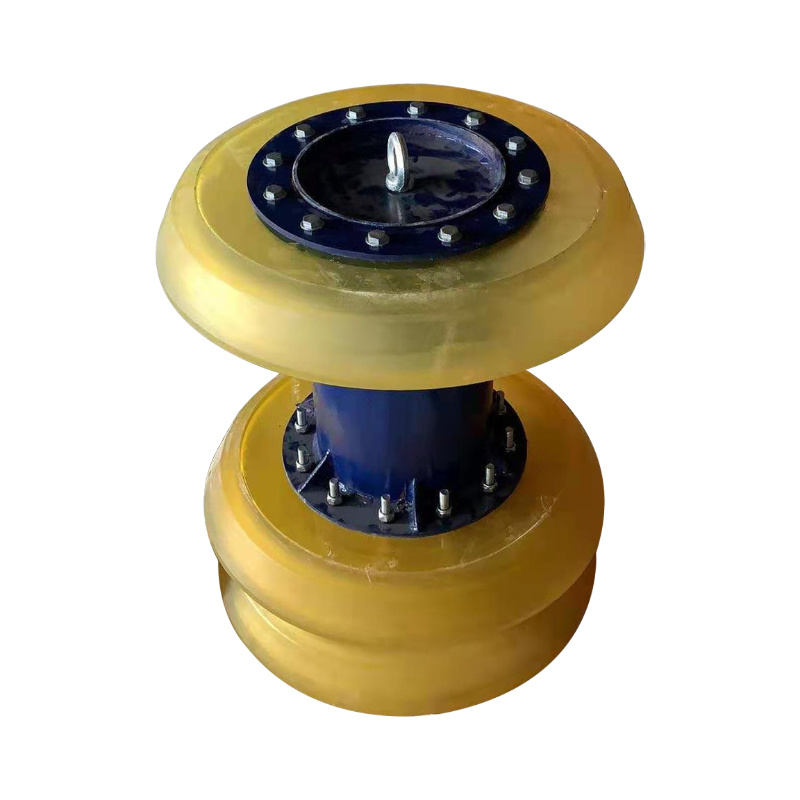
How to Optimize Your Pipeline with Oil Pipeline Sealing Pluggers
Table of Contents
- 1. Introduction to Oil Pipeline Sealing Pluggers
- 2. Understanding Oil Pipeline Sealing Pluggers
- 3. Optimizing Your Pipeline with Sealing Pluggers
- 4. Advanced Techniques for Enhanced Performance
- 5. Case Studies: Successful Implementations
- 6. Frequently Asked Questions
- 7. Conclusion
1. Introduction to Oil Pipeline Sealing Pluggers
In the world of oil transportation, ensuring the integrity of pipeline systems is paramount. One of the most effective tools in maintaining this integrity is the **oil pipeline sealing plugger**. These specialized tools are designed to prevent leaks, enhance efficiency, and prolong the life of pipeline systems. In this article, we delve into the various aspects of sealing pluggers, their benefits, and how to optimize their use in your pipeline operations for maximum efficiency.
2. Understanding Oil Pipeline Sealing Pluggers
2.1 What are Sealing Pluggers?
**Sealing pluggers** are mechanical devices used to block or seal off sections of a pipeline. They are essential for maintenance activities, preventing fluid loss, and minimizing the environmental impact of leaks. These devices come in various designs and materials, catering to different pipeline applications and fluid types.
2.2 Benefits of Using Sealing Pluggers
Utilizing sealing pluggers in your pipeline systems offers numerous benefits, including:
1. **Leak Prevention**: Sealing pluggers effectively prevent leaks, ensuring that fluids remain contained within the pipeline.
2. **Cost Savings**: By reducing the chances of leaks, sealing pluggers help save costs related to repairs, environmental cleanup, and regulatory fines.
3. **Maintenance Efficiency**: They allow for easier maintenance by isolating sections of the pipeline, enabling repairs without halting the entire system.
4. **Enhanced Safety**: Sealing pluggers contribute to a safer working environment by minimizing the risk of hazardous spills and accidents.
3. Optimizing Your Pipeline with Sealing Pluggers
To truly harness the power of sealing pluggers, implementing optimization strategies is crucial. Here are effective methods to ensure your pipeline systems operate at their best.
3.1 Installation Techniques for Sealing Pluggers
Proper installation of sealing pluggers is vital for achieving optimal performance. Follow these steps for effective installation:
- **Evaluate Pipeline Conditions**: Before installation, assess the condition of the pipeline and choose the appropriate plugger type based on pressure, temperature, and fluid characteristics.
- **Follow Manufacturer Guidelines**: Always adhere to the manufacturer's guidelines regarding installation processes to ensure a secure fit and effective sealing.
- **Use Appropriate Tools**: Utilize the right tools and equipment for installation, ensuring that the sealing plugger is positioned correctly within the pipeline.
3.2 Maintenance Tips for Longevity
Maintenance is key to prolonging the life of sealing pluggers and ensuring their effectiveness. Consider the following tips:
- **Regular Inspections**: Schedule routine inspections to check for signs of wear, damage, or leaks, allowing for timely repairs or replacements.
- **Clean the Pipeline**: Keeping the pipeline free from debris and contaminants will extend the life of your sealing pluggers.
- **Monitor Pressure Levels**: Regularly monitor pressure levels within the pipeline to detect any irregularities that may indicate a malfunctioning plugger.
4. Advanced Techniques for Enhanced Performance
To further optimize your pipeline, consider incorporating advanced techniques that leverage technology and data analysis.
4.1 Monitoring Systems and Data Analysis
Investing in advanced monitoring systems can significantly enhance the performance of oil pipeline sealing pluggers. These systems allow for:
- **Real-Time Data Tracking**: Monitor pressure, temperature, and flow rates in real-time to detect anomalies quickly.
- **Predictive Maintenance**: Use data analytics to predict potential failures or maintenance needs, allowing for proactive interventions.
4.2 Troubleshooting Common Issues
Even with the best practices in place, issues may arise. Here’s how to troubleshoot common sealing plugger problems:
- **Identify Leak Sources**: If leaks occur, use pressure testing to identify the exact location of the leak and determine whether the plugger needs adjustment or replacement.
- **Check Installation Integrity**: Ensure that the sealing plugger is correctly installed and that there are no obstructions or misalignments affecting its performance.
5. Case Studies: Successful Implementations
To illustrate the effectiveness of sealing pluggers, let's explore a few case studies that showcase their successful applications:
- **Case Study 1: Oil Refinery Optimization**
An oil refinery implemented sealing pluggers during a system overhaul. By isolating sections of the pipeline, they could conduct repairs without significant downtime. The result was a 30% reduction in maintenance costs over the following year.
- **Case Study 2: Environmental Compliance**
A pipeline operator faced regulatory scrutiny due to multiple leaks. By integrating high-quality sealing pluggers throughout the system, they not only achieved compliance but also enhanced operational efficiency, leading to increased profits.
6. Frequently Asked Questions
**Q1: What materials are sealing pluggers made from?**
A1: Sealing pluggers are typically made from materials such as rubber, plastic, or metal, depending on the specific requirements of the pipeline and the fluids being transported.
**Q2: How often should sealing pluggers be replaced?**
A2: The replacement frequency depends on factors such as pipeline conditions, fluid types, and operational pressures. Regular inspections can help determine when replacements are necessary.
**Q3: Can sealing pluggers be used in high-pressure systems?**
A3: Yes, there are sealing pluggers specifically designed to withstand high-pressure environments. It is essential to choose the right plugger based on the system's specifications.
**Q4: What should I do if a sealing plugger fails?**
A4: If a sealing plugger fails, isolate the affected section of the pipeline and conduct an inspection to identify the cause of the failure. Replace the plugger as needed and ensure proper installation.
**Q5: Are sealing pluggers environmentally friendly?**
A5: Many sealing pluggers are designed with environmentally friendly materials and features to minimize the risk of leaks, contributing to safer operations in sensitive areas.
7. Conclusion
Optimizing your pipeline with oil pipeline sealing pluggers is crucial for maintaining operational efficiency, reducing costs, and ensuring environmental safety. By understanding the functionality and advantages of sealing pluggers, implementing best installation and maintenance practices, and leveraging advanced monitoring techniques, you can significantly enhance the performance of your oil pipeline systems. Stay proactive in your approach, and your operations will not only meet but exceed industry standards.