Understanding the Different Materials Used in Oil Pipeline Sealing Pluggers
Jul 23,2025
Understanding the Different Materials Used in Oil Pipeline Sealing Pluggers
Table of Contents
1. Introduction to Oil Pipeline Sealing Pluggers
2. Importance of Sealing in Oil Pipelines
3. Types of Materials Used in Sealing Pluggers
3.1 Rubber Materials
3.2 PTFE (Polytetrafluoroethylene)
3.3 Metal Alloys
3.4 Composite Materials
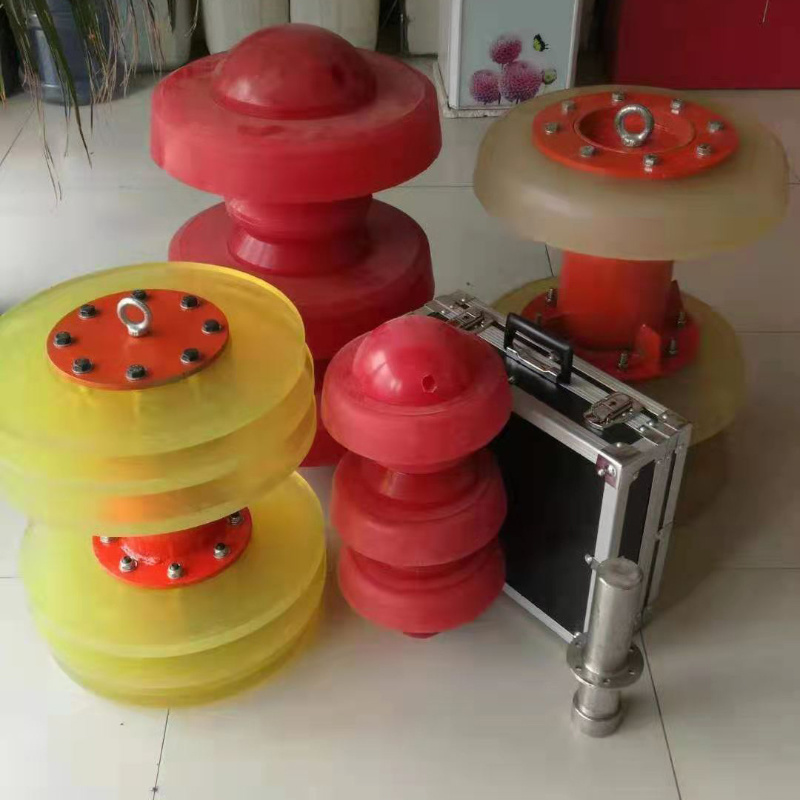
Understanding the Different Materials Used in Oil Pipeline Sealing Pluggers
Table of Contents
- 1. Introduction to Oil Pipeline Sealing Pluggers
- 2. Importance of Sealing in Oil Pipelines
- 3. Types of Materials Used in Sealing Pluggers
- 4. Applications of Sealing Pluggers in Oil Pipelines
- 5. Performance Characteristics of Different Materials
- 6. Safety Considerations in Material Selection
- 7. Maintenance of Pipeline Sealing Pluggers
- 8. Future Trends in Sealing Plugger Materials
- 9. Frequently Asked Questions (FAQs)
- 10. Conclusion
1. Introduction to Oil Pipeline Sealing Pluggers
Oil pipeline sealing pluggers play a critical role in maintaining the integrity of oil pipelines. These devices are designed to prevent leaks and ensure the safe transportation of oil from one location to another. The choice of materials used in these sealing solutions significantly affects their longevity, effectiveness, and adaptability to various pipeline conditions.
2. Importance of Sealing in Oil Pipelines
Sealing oil pipelines is crucial for several reasons:
- **Leak Prevention**: Oil leaks can lead to environmental disasters, affecting wildlife and ecosystems. Effective sealing prevents such occurrences.
- **Operational Efficiency**: Properly sealed pipelines maintain pressure and flow, ensuring that operations run smoothly without interruptions.
- **Cost Savings**: Preventing leaks reduces the potential for costly repairs and environmental cleanup efforts.
3. Types of Materials Used in Sealing Pluggers
Selecting the right material for sealing pluggers is essential for performance. Here, we explore the various materials commonly used in the industry.
3.1 Rubber Materials
Rubber is one of the most widely used materials in sealing pluggers due to its elasticity and compressibility. Its ability to conform to irregular surfaces makes it ideal for creating a tight seal. Additionally, rubber materials possess excellent resistance to various oils and chemicals, making them suitable for oil pipelines.
Types of rubber used include:
- **Nitrile Rubber**: Known for its oil resistance, nitrile rubber is commonly used in sealing applications where exposure to oil is prevalent.
- **EPDM Rubber**: This material excels in high-temperature environments and offers good resistance to weathering and ozone.
3.2 PTFE (Polytetrafluoroethylene)
PTFE is renowned for its chemical resistance and low friction properties. This makes it a preferred choice for sealing applications in harsh environments. PTFE seals are non-reactive and can withstand a wide range of temperatures, ensuring their reliability in oil pipelines.
Advantages of PTFE include:
- **High Thermal Stability**: PTFE can maintain its properties in extreme temperatures, making it suitable for various operational conditions.
- **Non-stick Properties**: The non-adhesive surface of PTFE aids in reducing friction, ensuring smoother operation in pipelines.
3.3 Metal Alloys
While rubber and PTFE are common, metal alloys also play a significant role in sealing solutions. Metal sealing pluggers are often used in high-pressure and high-temperature environments where other materials might fail.
Examples of metal alloys used include:
- **Stainless Steel**: Corrosion-resistant and durable, stainless steel is ideal for environments that pose a risk of corrosion.
- **Copper Alloys**: Copper offers excellent thermal conductivity and is often used in applications where heat dissipation is crucial.
3.4 Composite Materials
Composite materials combine the best properties of different materials to create a versatile sealing solution. These materials can be engineered to provide specific performance characteristics, such as enhanced strength or improved chemical resistance.
Common composite materials include:
- **Fiberglass Reinforced Plastics (FRP)**: These materials offer high strength-to-weight ratios and excellent chemical resistance.
- **Carbon Fiber Composites**: Known for their lightweight and high-strength properties, carbon fiber composites are emerging in sealing applications.
4. Applications of Sealing Pluggers in Oil Pipelines
Oil pipeline sealing pluggers are utilized in various applications, enhancing efficiency and safety. Key applications include:
- **Maintenance Plugging**: Used during maintenance operations to isolate sections of the pipeline, preventing oil from leaking.
- **Leak Repair**: In situations where a leak is detected, sealing pluggers can be deployed to temporarily seal the leak until permanent repairs are made.
- **Pressure Testing**: Sealing pluggers are essential in pressure testing pipelines, ensuring that they can withstand specified pressures without leaking.
5. Performance Characteristics of Different Materials
Understanding the performance characteristics of sealing materials is vital for ensuring the reliability of oil pipelines. Key performance indicators include:
- **Chemical Resistance**: The ability of a material to withstand exposure to oils and other chemicals without degrading.
- **Temperature Tolerance**: The range of temperatures a material can endure without losing its sealing properties.
- **Durability and Longevity**: The lifespan of sealing materials under continuous operational conditions.
6. Safety Considerations in Material Selection
Safety is paramount in the oil industry, and selecting the right materials for sealing pluggers is crucial. Considerations include:
- **Flammability**: Materials must be non-flammable to avoid fire risks in oil pipelines.
- **Toxicity**: Sealing materials should not release harmful substances into the environment in case of failure.
7. Maintenance of Pipeline Sealing Pluggers
Regular maintenance of sealing pluggers is essential for ensuring their long-term effectiveness. Best practices include:
- **Routine Inspections**: Regularly check sealing pluggers for signs of wear or degradation.
- **Replacement Protocols**: Establish a replacement schedule based on the materials used and operational conditions.
8. Future Trends in Sealing Plugger Materials
As technology evolves, so do the materials used in sealing pluggers. Future trends may include:
- **Smart Materials**: Development of materials that can self-heal or adapt to changing conditions in pipelines.
- **Biodegradable Options**: Increasing focus on environmentally friendly materials that reduce the ecological impact of oil spills.
9. Frequently Asked Questions (FAQs)
What are the most common materials used in oil pipeline sealing pluggers?
The most common materials include rubber, PTFE, metal alloys, and composite materials, each offering unique benefits depending on the application.
How do environmental conditions affect the choice of sealing materials?
Environmental conditions, such as temperature, pressure, and exposure to chemicals, greatly influence the selection of sealing materials to ensure optimal performance.
What is the lifespan of sealing pluggers?
The lifespan of sealing pluggers varies based on the material used and the operational conditions, but regular maintenance can significantly extend their durability.
Can sealing pluggers be reused?
In some cases, sealing pluggers can be reused, but this depends on the condition of the plugger after use. Thorough inspections are necessary before considering reuse.
How do I know if my pipeline needs sealing pluggers?
Signs of leaks, pressure drops, or unusual noises in the pipeline may indicate the need for sealing pluggers. Regular monitoring and maintenance can help identify these issues early on.
10. Conclusion
Understanding the different materials used in oil pipeline sealing pluggers is essential for maintaining the integrity and safety of oil transportation systems. Each material offers unique properties that can be leveraged to enhance performance, ensuring effective sealing solutions. By staying informed about the latest advancements and best practices in material selection and maintenance, operators can safeguard their pipelines against leaks and other potential hazards. As the industry evolves, keeping an eye on future trends will allow for continued innovation in sealing technology, ultimately contributing to the safety and efficiency of oil pipelines worldwide.
PREVIOUS: